Shina Mechanical Equipment Co., Ltd!
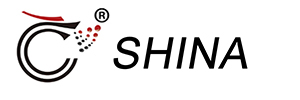
Polishing powder material
1. Polishing powder material
Polishing powder is usually composed of cerium oxide, alumina, silicon oxide, iron oxide, zirconia, chromium oxide
and other components. Different materials have different hardness and different chemical properties in water, so
the use occasions are different. Alumina and chromium oxide have a Mohs hardness of 9, ceria and zirconia 7, and
iron oxide is even lower. Cerium oxide is used in glass polishing because of its high chemical activity and comp
-arable hardness with silicate glass.
2. Basic requirements for polishing powder
(1) The particle size of the micro-powder is uniform and consistent, within the allowable range;
(2) high purity, no mechanical impurities;
(3) It has good dispersion and adsorption to ensure the uniformity and efficiency of the processing process. LBD-1
dispersant can be added appropriately to improve the suspension rate;
(4) The powder particles have a certain lattice shape, forming sharp sharp corners when broken to improve the poli
-shing efficiency;
(5) It has appropriate hardness and density, and it has good wettability and suspension with water, because the poli
-shing powder needs to be mixed with water
3. Granularity of cerium oxide
The larger the particle size of cerium oxide, the greater the grinding force, the more suitable for harder materials,
ZF glass should use a finer polishing powder. It should be noted that the particle size of all ceria has a distribut
-ion problem. The average particle size or median diameter D50 only determines the polishing speed, while the partic
-le size Dmax determines the polishing accuracy. Therefore, the particle of polishing powder must be controlled to
obtain the high precision requirement.
Its processing technology is: by roasting after superfine grinding or superfine classification
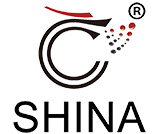
Tel.: 0086 158 5326 1107
Email: sales@qdshina.com
Address: 207 Shenzhen South Road, Laixi, Qingdao city, China.
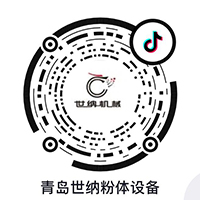
Tiktok
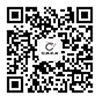

国内销售部:0532-88413877
国际销售部:15853261107
技术部:15853227399
售后:15725258766
邮箱:sales@qdshina.com
地址:青岛莱西市深圳南路207号
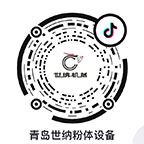
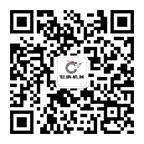
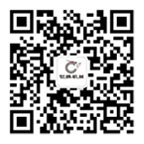